Twin Screw Extruders Applications
Compounding & Pelletizing Process

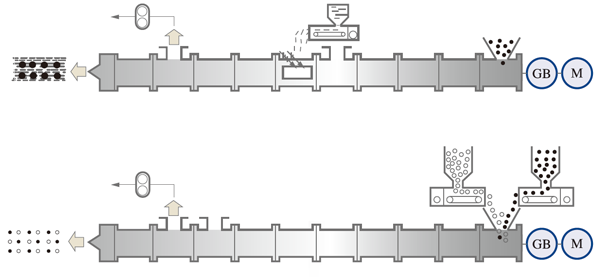
Resin example: commodity resin / engineering plastic / super engineering plastic /
biomass plastic / biodegradable plastic / various fillers / various liquids / various crushed products
Out put(Reference)

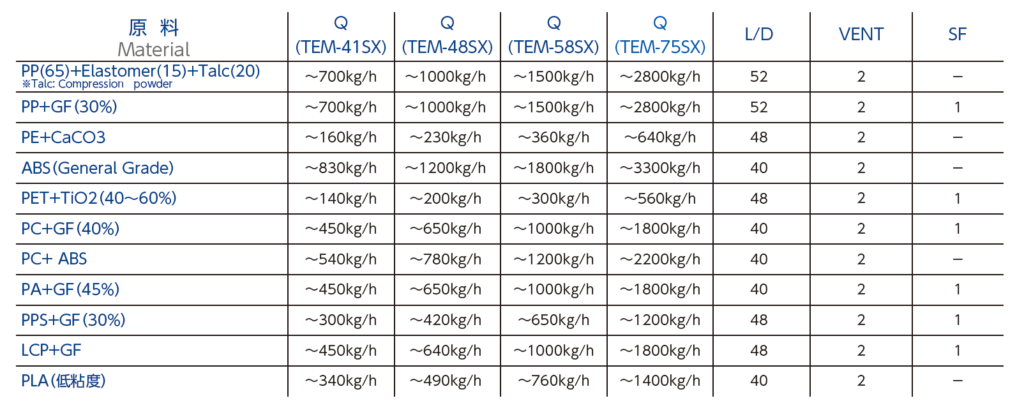
Dewatering Process

Dewatering system of ABS wet powder and rubber (TPE, SBR, EPR, AR) is one of our special different technology. it si sometimes called squeezer or dryer and it demonstrates. It prevents the equipement investment and helps to improve the productivity and drives down the running cost. Also it corresponds to enviromental loading reduction(e.g. VOC, and others).

Devolatilizing Procces

It corresponds to solid-feed and melt-feed, and it rids the residual monomer and solvent continuously to the limit. The adoption of the water stripping method, special vent, and so on, realized an efficient devolatilizing system. We could support you by the devolitizing simulation system which is based on the experience and results.
Reactive Process

You can use it for the reacter of polymerization, depolymerization, and chemical reforming of the material which needs detention time. Twin screw extruder has very high productivity than batch type and the self-cleaning effect of the screw makes it possible to reduce the gel occur. We could support various type reactive extrusion based on merit have L/D=100 Based on the result of L/D=100, we could support various type reactive extrusion.

Direct Extrusion Process

Direct extrusion Process of sheet and film using twin screw extruder without pelletizing or drying process could improve the quality by deterriolation inhibition, and saves the energy and space. Operating range is wider than the single screw extruder, and it contributes to productibity by rasing ratio of fluff. Also the segment method screw could correspond to various types of resin, and therefore application range expands.
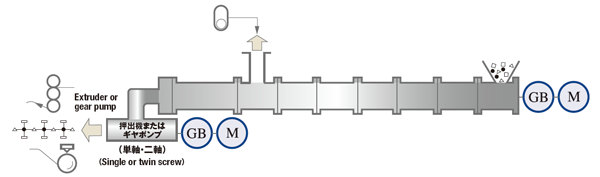
environment-friendly

Our twin-screw kneading extruders are developed with consideration for the environment.
Recycle
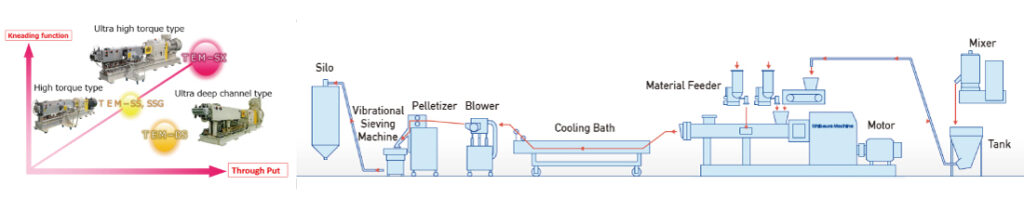
Shibaura Machine proposes diversified recycling compounds such as material recycling and chemical recycling with the optimum equipment configuration using the twin-screw kneading extruder “TEM”.
- Optimization of specifications using extensive test facilities
- Applying conventional engineering capabilities to recycled compounds
- Extensive line-up for various recycled raw materials
- It is possible to select a model according to the purpose, such as increased discharge by increasing
- the biting amount, kneading at low temperature, etc.
- Many achievements in various fields such as home appliances, automobile parts, food containers, optical films, etc.

CNF Compound

We are proposing the optimization of CNF, a new material, in combination with each raw material.
We conduct tests jointly with each user.
- Device configuration example
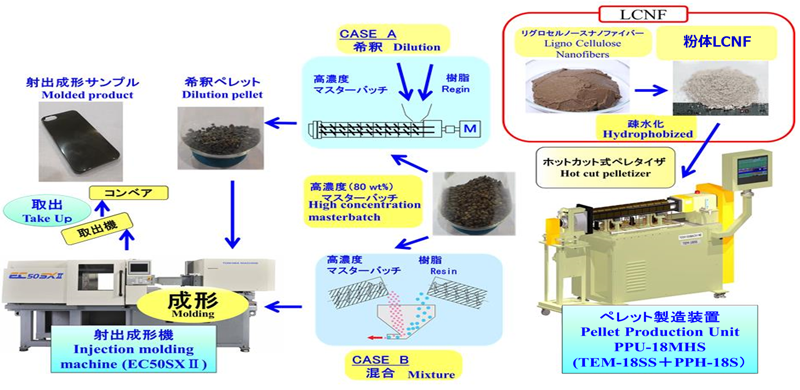
●Test performance at our company (example) Test example
① Raw material: Olefin (PP powder)
CNF (wet powder) ※Blended in a mixer
Product: CNF content (5wt%)
Test purpose: Both dehydration and dispersion Test example
② Raw material: Olefin (PP/LDPE)
CNF (2wt% aqueous solution)
Product: CNF content (0.2wt%)
Purpose of test: Improving secondary moldability and fluidity Test example
③ Raw material: PLA + CNF 0.5% aqueous solution
Test purpose: Confirmation of improvement in physical properties Test example
④ Raw material: CNF + surfactant
Test purpose: defibration of CNF